
CLEANING PERFORMANCE COMPARISON
SootGone™
High Cleaning Performance:
-
The velocity of the hot and dry wave produced by SootGone™ is about 3MACH (1300m/sec).
-
The wave duration is milliseconds.
-
The mass of blast wave created by Pulse Generator is insignificant: about 250 grams omnidirectionally.
-
The cleaning efficiency distance is large with reflections and diffractions.
Why is SootGone™ effective and harmless to the boiler?
The low mass and high velocity of the omnidirectional wave-pulse generated from the detonation is the source of Soot Gone™ effectiveness in boiler cleaning.
The physical meaning of pulse is: F x T = M x V
(F-force; T-time; M-mass; V-velocity)
Such pulses are effective in cleaning and harmless to the tubes, refractories and boiler structure.
An impulse wave spreads in the boiler volume omnidirectionally and removes the ash from the heat-transfer surfaces circumferentially.
SootGone™ is more effective than other alternatives. Each Pulse Generator can clean a relatively large area and reach areas inaccessible to conventional soot blowers.
Steam Soot Blower
Low Cleaning Performance:
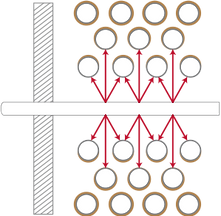
-
Narrow angle steam jets with a speed of approx. 300 m/s with the possibility of cleaning at a short distance.
-
Conventional steam soot blowing technology is limited to line-of-sight cleaning.
Steam potentially introduces excessive moisture and condensation in the boiler, with accompanying damage to the pipes, supports, and refractories (thermos shock phenomena).
APPLICABILITY COMPARISON
The SootGone™ system can be applied to the following areas:
-
evaporators
-
economizers
-
superheaters
-
air preheaters
-
ducts
-
hoppers
-
chimneys
The hot blast wave of supersonic velocities and relatively large distance effect makes it possible to clean ducts, hoppers and chimneys from deposits avoiding refractories damaging.
-
Hard to reach areas.
The installation flexibility due to its small footprint allows Soot Gone™ to be installed in a variety of locations, including hard-to-reach areas.
The SootGone™ system is capable of removing the following sedimentation types :
-
ash
-
soot
-
slag
-
cement
-
lime
-
pigments
-
additives
-
fertilizers, etc.
SootGone™ operates with hot and dry gases, that is why it can be used to clean the surfaces from different powder deposits like pigments, additive products, cement, lime, etc., where moisture is unacceptable.
Steam Soot Blower is capable of removing the following sedimentation types:
-
ash
-
soot
-
slag
Not suitable for cleaning cement, lime, pigments, additives, fertilizers.
Contact of such materials with steam leads to sintering and other undesirable phenomena.

Steam Soot Blower can be applied to the following areas:
-
economizers
-
superheaters
-
air preheaters
Not suitable for cleaning ducts, hoppers, and chimneys.
High humidity short distance steam jets are inefficient and cause thermal shocks and slag sintering.
Limited installation and use in hard-to-reach areas due to significant dimensions of Steam Soot Blowers with their huge service platforms.
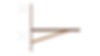
The SootGone™ system can be used in corrosive environments.
There's no wear and tear in Soot Gone™ due to the fact that it is outside the boiler.
Steam Soot Blower is not applicable in corrosive environments.
Steam Soot Blower's lance traverses inside the boiler which leads to its rapid erosion and corrosion.
INSTALLATION COST
High installation cost:
-
requires large service platforms spaces;
-
requires laying cables along the walls of boilers.
Low installation cost:
-
compact;
-
no need in wide service platforms;
-
no need for electrical or instrumentation cables on boiler body;
-
flexible and easy in installation.
SootGone™
Steam Soot Blower
MAINTENANCE COST
SootGone™
Steam Soot Blower
Low maintenance cost:
-
no moving parts-static device;
-
no internal components inside the boiler;
-
almost no need in spare parts in the stock;
-
high level of reliability.
High maintenance cost:
-
wear items: housing, gearbox seals,
feed tubes, blown and damaged nozzles,
worm and damaged carriage housing,
warped, melted and corroded lance tubes,
entangled cable and power cords, worn and failed gearbox seals, corroded feed tubes, motors and gears, steam traps, packing tensioner, etc. -
A great amount of spare parts is needed in stock which value reaches hundreds of thousands of $.
BOILER DAMAGE
SootGone™
Steam Soot Blower
Operating SootGone™ doesn't damage the boiler.
The actuating medium is hot flue gases.
No moisture or condensate is injected inside the boiler.
The mass of blast wave created by Pulse Generator is insignificant: about 80 grams omnidirectionally.
Such high velocity low mass pulses are effective in cleaning and harmless for the tubes, refractories and boiler structure.
Operating Steam Soot Blower can damage the boiler:
-
high steam humidity causes the thermal shock and corrosion in boiler structure and refractories;
-
pipe’s additional corrosion inside the boiler;
-
refractory ‘s erosion;
-
boiler structure damage;
-
damage to the boiler pipe supports;
-
ash deposit accumulation.
OPERATION COST
Cycles per day 10
Cost per cycle $ 0.06
Cost per Day /Blower $ 0.6
Operating days per year 330
Annual cost per blower $ 198
Qty of blowers per boiler 30
Annual blowing cost for boiler $ 5,940
Cycles per day 10
Cost per cycle $ 3.30
Cost per Day /Blower $ 33
Operating days per year 330
Annual cost per blower $ 10,890
Qty of blowers per boiler 30
Annual blowing cost for boiler $ 326,700
SootGone™
Steam Soot Blower